Product Features
The high-quality aluminum veneer curtain wall is processed with fluorocarbon spraying on the surface, making it resistant to ultraviolet light, temperature, air erosion and atmospheric corrosion. It not only has excellent bending resistance and wind resistance, but also showcases its characteristics through secondary development. The aluminum curtain wall veneer possesses the following features: lightweight, high strength, waterproof and anti-pollution properties, fireproof corrosion resistance, excellent processing performance, low maintenance cost and long lifespan. The veneer can be shaped into various curved forms and painted in different colors to create beautiful patterns on the wall when compared to glass curtain walls, giving buildings a more noble and elegant appearance.
SURFACE TREATMENT OF SINGLE PANEL OF ALUMINUM CURTAIN WALL
The panel curtain wall is typically treated with chromating followed by a Fluorocarbon coating. The Fluorocarbon coating finish paint, made of Polyvinylidene fluoride resin (KYNAR500), is applied in 2, 3, or 4 layers to provide outstanding corrosion and weathering resistance, as well as protection against acid rain, salt fog, and air contaminants. Additionally, it offers excellent thermal and cold endurance, strong ultraviolet resistance, long-lasting color retention without pulverization for an extended service life. Our factory uses high-quality fluorine carbon coating materials from reputable manufacturers such as PPG, NDT, AKZO., and NIPPO., offering a wide range of colors for customers to choose from according to the manufacturer’s color plate or by providing a color sample.
MATERIALS AND CONSTRUCTION OF ALUMINUM VENEER CURTAIN WALL
The aluminum veneer curtain walls are constructed using high-quality, high-strength aluminum plates with a common thickness of 2.0mm, 2.5mm, or 3.0mm and models including 1100 and 3003 in the H24 state. The maximum dimension for the general material is 1300mm x 4000mm, while unconventional materials can be as large as 2200mm x 6000mm. The structure consists of a front panel, reinforced rib, and corner brace which can be formed by panel bending and punching or riveting on the hem of the panel. The reinforced rib is securely joined with electric welding bolts behind the plate to ensure strength, rigidity, flatness, wind resistance, and shock resistance during long-term use. Additional sound insulation and heat preservation effects can also be added inside the aluminum sheet.
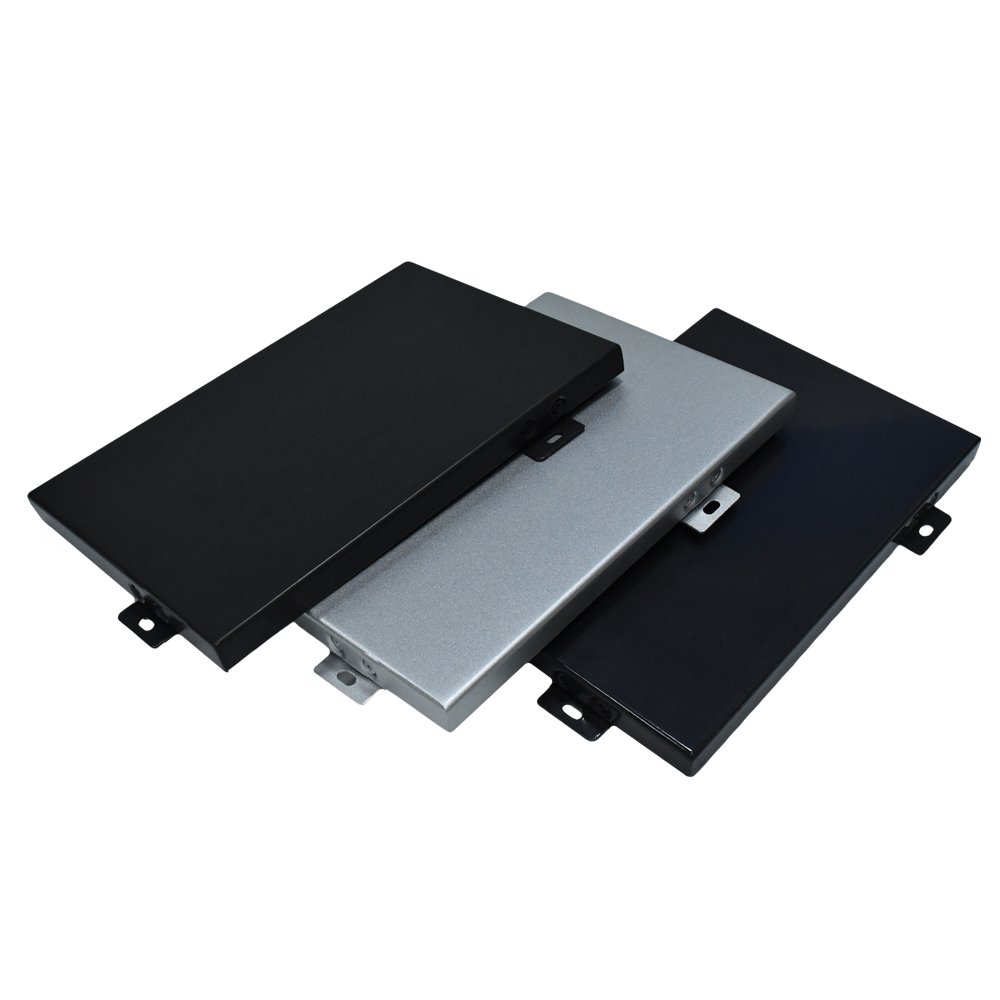